BOSTON, Dec. 3, 2020 /PRNewswire/ — We are often told that ‘you can’t have your cake and eat it.’ However, many technological advancements succeed commercially precisely because they eliminate an existing compromise. Flexible hybrid electronics (FHE) is a great example of an emerging technology that removes a previous trade-off, specifically between the flexibility of printed electronics and functionality of conventional PCBs, and is thus rapidly gaining traction.
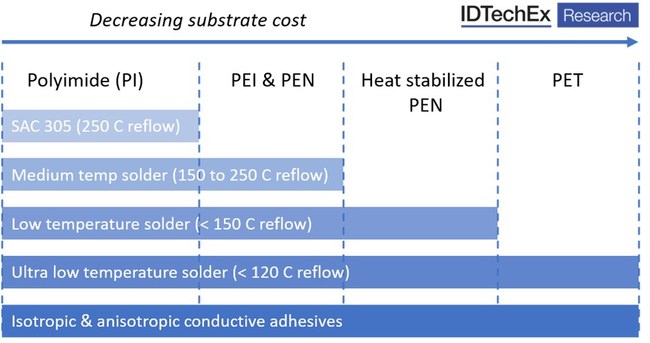
Indeed, IDTechEx CEO Raghu Das states that “There is rapidly increasing interest in flexible hybrid electronics – this is an approach that resolves the downsides of fully printed electronics and will ultimately be employed across many sectors.”
An FHE circuit is an elegant compromise that uses printed conductive interconnects, antennas, and possibly sensors, while mounting complex components such as integrated circuits. The overarching principle is perhaps best expressed as ‘print what you can, place what you can’t.’ FHE has applications across multiple sectors ranging from wearable technology to smart packaging and is estimated by IDTechEx to be an approximately $3 billion market by 2030. More information about FHE, including technological challenges, innovation opportunities and application case studies can be found in the IDTechEx research report: “Flexible Hybrid Electronics 2020-2030: Applications, Challenges, Innovations and Forecasts“.
Required: Innovative component attachment materials
Despite the promise of and the commercial interest in FHE, some technological challenges remain. One of the most important is developing the ability to robustly attach mounted components to flexible substrates, given the substantial difference in mechanical and thermal properties. Furthermore, component attachment materials must have curing/reflow temperatures that are compatible with thermally fragile low-cost flexible substrates such as PET and PEN. Conventional solder with a reflow temperature of 250°C can only be used with expensive polyimide (PI), leading to the orange color that characterizes the current generation of flexible PCBs.
Given this clear market need, a range of innovative component attachment materials are being developed (Figure 1). These include low-temperature solders with reflow temperatures compatible with low-cost polymeric substrates and field-aligned anisotropic conductive adhesives that enable components with closely spaced contacts to be mounted more rapidly.
Low temperature solder
Perhaps the most straightforward solution to the issue of high reflow temperatures is simply to produce solder with a lower temperature by changing the alloy composition. Solder companies are developing both low temperature (reflow < 170 C) and ‘ultra-low temperature’ solder (reflow < 150 C), with the latter explicitly targeted at attaching components to cheap transparent PET substrates, and thus for flexible hybrid electronics. Although the precise compositions are not publicly disclosed, low-temperature solder alloys often include a substantial proportion of bismuth, which can make connections mechanically brittle.
An arguably more innovative approach to low-temperature solder has been developed by an early stage US company that has developed nanoparticles that contain supercooled liquid solder. This enables the solder flow to be achieved without heat, with either mechanical force or chemicals breaking the outer shell and enabling the previously encapsulated liquid solder to flow.
Conductive adhesives
An alternative to solder that does not require reflow is conductive adhesive, which can be either isotropic or anisotropic. Isotropic conductive adhesives (ICAs) conduct in all directions and are suitable for LEDs, resistors, capacitors. The adhesive needs curing, usually thermally (although UV is also possible), although the temperature requirements are much lower than conventional solder. An example application is bonding RFID ICs to antenna since high throughput is essential and resolution requirements are relatively low as the ICs only have two I/O pads.
Anisotropic conducting adhesives (ACAs) are more complex materials that conduct only in the z-axis. They are especially applicable for IC attachment, where applying individual dots of an ICA to I/O pads with a fine pitch may be challenging and thus risk a short circuit. In contrast, ACAs can be deposited in a homogeneous layer because conductivity is only in the z-axis and are therefore often available as films rather than pastes. ACAs also need heat and pressure to form a vertical electrical pathway by trapping the conductive particles embedded in the epoxy between the contacts. There is currently substantial innovation in ACAs, with self-assembly under magnetic or electric fields improving conductivity and reducing the temperature and pressure requirements. Expect to see increased adoption of ACAs as ICs with more I/O ports are incorporated within FHE circuits.
Readiness level assessment
The emerging component attachment materials discussed above are at different levels of technological and commercial readiness. Field-aligned ACAs are expected to be used in commercial production sometime in 2021.
In summary, as electronics expand into new applications with novel form factors for FHE, the conventional rigid circuit board will no longer be the default format. Using a wider range of substrates, in particular flexible polymeric substrates, will require a range of alternatives to conventional SAC solder. Reducing reflow/curing temperatures will assist higher throughput manufacturing, especially R2R processing while reducing the minimum pitch will simplify IC packaging and potentially enable connections with bare dies. For anyone in the electronics industry, the evolution of component attachment materials beyond conventional solder, especially in the context of FHE, is certainly well worth watching.
IDTechEx offers a wide range of technical market research reports covering most aspects of printed/flexible electronics, including “Flexible Hybrid Electronics 2020-2030: Applications, Challenges, Innovations and Forecasts“. The latter report covers a wide range of functional materials, including materials for organic light emitting diodes (OLEDs), photovoltaics (OPV), thin film transistors (OTFTs), photodetectors (OPDs), along with carbon nanotubes, perovskites, quantum dots, functional inorganic inks, component attachment materials and conductive inks.
All IDTechEx printed/flexible electronics reports build on a long history of analyzing these technologies, markets, and applications and include detailed analysis of established and emerging technologies, their potential adoption barriers and suitability for different applications, and an assessment of technological and commercial readiness. IDTechEx reports also include multiple company profiles based on interviews with early-stage and established companies, along with 10-year market forecasts. For more information on this report, please visit www.IDTechEx.com/FlexElec or for the full portfolio of PE research available from IDTechEx please visit www.IDTechEx.com/research/PE.
IDTechEx guides your strategic business decisions through its Research, Subscription and Consultancy products, helping you profit from emerging technologies. For more information, contact [email protected] or visit www.IDTechEx.com.
Image download: https://www.dropbox.com/sh/3f0hj2unh8w9jem/AAAtmQqcKRl_OZq__LhiIpTUa?dl=0
Media Contact:
Natalie Moreton
Digital Marketing Manager
[email protected]
+44(0)1223 812300
Social Media Links:
Twitter: https://www.twitter.com/IDTechEx
LinkedIn: https://www.linkedin.com/company/idtechex/
Facebook: https://www.facebook.com/IDTechExResearch
SOURCE IDTechEx